TRIART Corporation (Headquarters: Iizuka City, Fukuoka Prefecture, CEO: Kentaro Imazu, hereinafter referred to as TRIART) and Toyota Motor Kyushu, Inc. (Headquarters: Miyawaka City, Fukuoka Prefecture, President: Osamu Nagata, hereinafter referred to as Toyota Kyushu) will initiate the operation of a priority traffic control system that forms a “ring network,” where vehicles equipped with participating terminals are connected in a circular manner and communicate directly with each other, performing mutual safety checks In long-distance unmanned transport vehicles used outdoors at the Toyota Kyushu Miyata Plant, which manufactures Lexus. The plan is to operate a single system that monitors the movement of outdoor long-distance unmanned transport vehicles, controls priority traffic at intersections, and confirms safety with pedestrians.
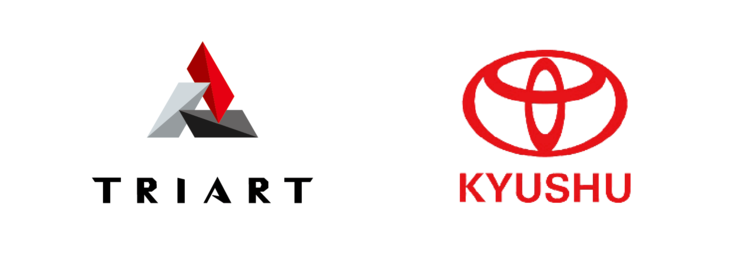
In manufacturing plants across various industries today, there is an increasing trend of adopting unmanned transport vehicles (Automatic Guided Vehicle, AGV) for the on-site transportation of products and parts. AGVs typically navigate according to some form of guidance such as magnetic lines, QR codes, or RFID, and equipped with a function to avoid collisions through onboard sensors. Even in automobile factories with vast premises, they have become indispensable in many places as a measure to reduce the workload on workers and improve productivity. However, until now, complex layouts where crossing and merges occur could only be operated with scheduled runs that fully managed the travel sequence, and this was limited to cases where all AGVs were centrally managed on the same system by the same manufacturer.
TRIART has successfully developed a “priority traffic control system” that enables vehicles to autonomously determine priority at intersections, assuming the Toyota Kyushu’s Miyata Plant where AGVs from multiple manufacturers operate with their own data formats and communication specifications. Starting from January 2022, it is planned to begin the operation of movement monitoring for long-distance unmanned transport vehicles traveling outdoors in certain sections of the Miyata Plant using a similar system.
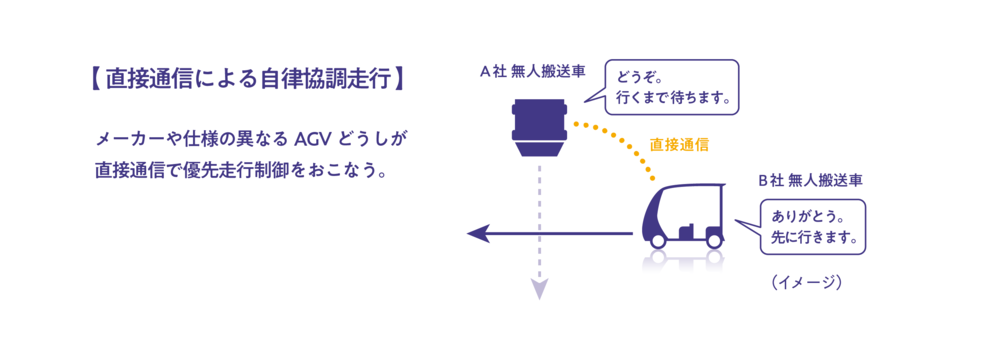
These are interactive systems where AGVs from different manufacturers communicate directly without infrastructure, representing an innovative architecture that enables autonomous coordination while absorbing the differences in specifications of vehicles from each manufacturer, pedestrian terminals, and potentially road infrastructure infrastructure and similar equipment in the future.This mechanism is realized mainly through the following two proprietary developments.
【1】Forming a ring network that allows various terminals to join and leave
They equips agents of TRIART’s proprietary distributed computing technology, “XCOA *” in various devices (in-vehicle smartphones, worker smartphones, administrator PCs, etc.), forming a “ring network” that connects through direct device-to-device communication (P2P communication). The ring itself is as an autonomous network and also functions as a single computer executing programs such as the “priority traffic determination logic” as in this case. so then unlike centralized monitoring/control by servers, this setup does not impose communication load on real-time processing or continuous operations. Additionally, it possesses redundancy that maintains communication even during the arbitrary joining and leaving of devices.
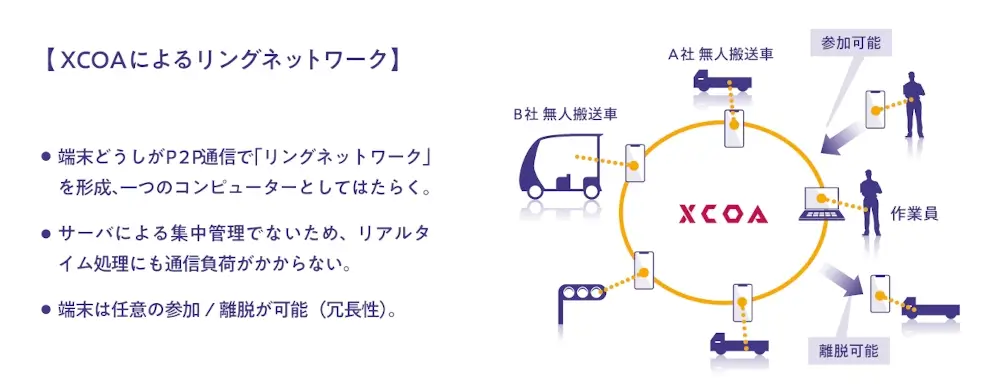
【2】Build collaboration functions with devices with different specifications
Results processed on the ring network (such as stop commands) are messaged to AGV vehicles and AGV management devices, enabling control of each device (such as applying brakes to vehicles). Depending on the target of the messaging, it goes through a PLC (Programmable Logic Controller) or a ROS (Robot Operating System) machine. Differences in data formats and communication specifications due to various company standards are standardized (translated) here, and the judgment is entrusted to a common logic on the ring network, thus absorbing these differences.

Since the ring network, which is the foundation of this system, is based on P2P communication, it does not incur risks or costs associated with server load concentration. If you expand collaboration by increasing the number of rings according to the number and roles of participating devices, the strengths of distributed computing will be further leveraged as the scale expands. Furthermore, reducing the social cost of developing and maintaining software for unified standards and enabling flexible designs according to usage and environment are also advantages.
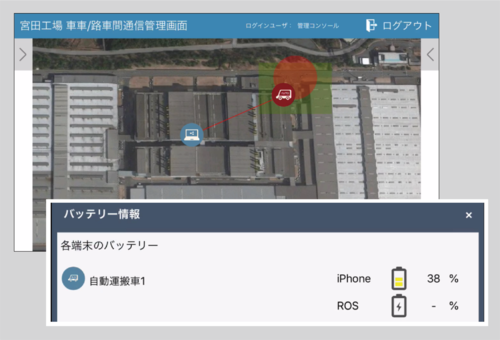
( Shown in the photo up ) A management interface where the movements of participating devices on the ring network can be monitored.
( Shown in the photo up ) Real-time monitoring of each device status such as battery levels.
The current operation primarily focuses on a small number of vehicles and collaborating workers, but there are plans to expand the system into a system in which people walking within the factory premises, and road infrastructure etc. can also participate in the future. At the Miyata Plant’s outdoor facility, within the 2.5 km outdoor facility, Ten types of transport vehicles are running to transport parts, and Each one runs at different timings and coexists with pedestrians, and trucks entering and exiting. Considering this, various patterns of intersections and merges occur in that area. If all of these transport vehicles were unmanned and could be controlled by mutual judgment without centralized management including pedestrians and facilities, the future that decentralized computing supports tthe general traffic infrastructure for autonomous vehicles to operate comes into view.
When introducing new societal infrastructure,while there are centralized methods that involve completely overhauling existing systems, ensuring performance by coordinating existing systems while simultaneously avoiding over-concentration of information and authority iis an important perspective to consider when thinking about the future of information technology. TRIART applies its in-house developed technology to explore its potential in various fields, while Toyota Kyushu takes the lead in generalizing new production technologies born from practical challenges in the field. Our system also will continue research and development to devolve into valuable technology for implementation in future society, building upon the practical application achieved this time.
*Distributed computing technology 「XCOA」= Cross Computing Architecture. “XCOA” is a registered trademark of TRIART Corporation and proprietary design technology (Japanese Patent No. 6427697 & 6427702 [International Patent Pending]).